Packaging Machine Repair Service: Avoid Costly Malfunctions with Professional Assistance
Packaging Machine Repair Service: Avoid Costly Malfunctions with Professional Assistance
Blog Article
Comprehending the Key Parts and Fixing Techniques for Packaging Maker Maintenance
Effective maintenance of packaging machines rests on a complete understanding of their vital components, including the frame, drive system, and securing devices. Acknowledging usual maintenance problems, coupled with the execution of preventative approaches and fixing strategies, can significantly enhance maker reliability. The option of fixing practices, including the use of OEM parts and the value of certified professionals, plays a crucial role in decreasing downtime. To absolutely grasp the details of these systems and their maintenance, one must think about the more comprehensive effects of neglecting these crucial methods.
Key Components of Packaging Equipments
Packaging equipments consist of several vital components that collaborate to guarantee effective and efficient packaging procedures. At the core of these makers is the structure, which gives structural stability and houses the different operating components. The drive system, typically a combination of equipments and electric motors, helps with the movement of elements, allowing precise procedure throughout the product packaging cycle.
An additional crucial part is the conveyor system, which transfers products through various phases of the packaging process. This is typically matched by sensors and controls that keep track of the placement and speed of items, ensuring synchronization and reducing mistakes. The filling system is crucial for accurately dispensing the best quantity of product into bundles, whether in liquid, powder, or solid form.
Sealing systems, consisting of warmth sealers or adhesive applicators, play a vital function in protecting plans, preventing contamination and expanding life span. In addition, classifying systems are essential for offering required item info, making certain conformity with guidelines. The control panel, furnished with user-friendly interfaces, allows operators to handle device functions, monitor performance, and make modifications as needed, making certain ideal efficiency and performance in product packaging procedures.
Usual Maintenance Concerns
Efficient operation of packaging devices counts heavily on routine maintenance to avoid usual issues that can disrupt manufacturing. Amongst these concerns, mechanical wear and tear is common, specifically in parts like seals, conveyors, and electric motors, which can result in unforeseen downtimes. In addition, misalignment of components can cause ineffective operation, creating items to be incorrectly packaged or damaged during the procedure.
One more usual upkeep problem includes the buildup of dirt and debris, which can interfere with the equipment's sensors and relocating parts. packaging machine repair service. This not just affects efficiency but can additionally present security risks. In addition, lubrication failings can result in boosted friction, causing overheating and eventual element failing.
Electric issues, frequently originating from loose connections or worn-out electrical wiring, can disrupt machinery functions, leading to substantial production delays. Lastly, software application glitches because of out-of-date programs or incorrect configurations can hinder the equipment's procedure, demanding immediate intervention. Resolving these typical maintenance issues proactively is vital for guaranteeing optimum performance and long life of packaging machinery.
Preventative Upkeep Techniques
Implementing preventative maintenance techniques is vital for maintaining the efficiency and reliability of product packaging equipments. These approaches incorporate an organized method to maintenance, concentrating on the routine inspection and maintenance of equipment to preempt prospective failures. By sticking to an arranged upkeep program, operators can recognize deterioration on components prior to they bring about significant failures.
Key elements of a preventative maintenance method include regular evaluations, component, cleaning, and lubrication replacements based on manufacturer recommendations. Utilizing lists can enhance this process, ensuring that no crucial jobs are forgotten. In addition, maintaining exact documents of upkeep tasks aids in tracking the maker's efficiency with time, helping with notified decision-making relating to future upkeep needs.
Educating personnel on the significance of preventative maintenance boosts conformity and fosters a society of aggressive care. Carrying out a predictive upkeep part, making use of data analytics and sensor innovation, can additionally enhance machinery performance by predicting failures before they occur.
Fixing Methods
When confronted with malfunctions or inadequacies in product packaging devices, using systematic troubleshooting methods is vital for determining and dealing with problems promptly. The initial step in reliable troubleshooting is to establish a clear understanding of the maker's operational parameters and efficiency metrics. This entails evaluating the maker's specs, along with any mistake codes or notifies presented.
Next, drivers should conduct a visual assessment, looking for obvious indications of damages, misalignment, or wear. This commonly includes analyzing equipments, belts, and sensors to pinpoint prospective reasons of breakdown. Gathering operational information, such as manufacturing prices and downtime logs, can also give understandings right into recurring concerns.
Once prospective issues are identified, using a sensible strategy to isolate the origin is vital. This might require screening private elements or systems in a regulated fashion. Involving in conversations with drivers who communicate with the machinery consistently can generate beneficial feedback about uncommon actions or patterns.

Fixing and Substitute Best Practices
A detailed understanding of repair service and replacement ideal methods is essential for preserving the longevity and effectiveness of product packaging machines. Routinely analyzing the problem of machine parts permits for timely intervention, preventing more significant problems that can lead to pricey downtimes.
When repair work are needed, it is necessary to use OEM (Original Equipment Manufacturer) parts to make sure compatibility and efficiency. This not only preserves the integrity of the maker but likewise promotes warranty arrangements. Additionally, it is advisable to preserve a supply of crucial extra components to promote fast replacements and reduce functional article source disruptions.
For complex repair services, involving certified specialists with specialized training in product packaging machinery is advised. They have the knowledge to identify concerns properly and execute repair work effectively. Recording all fixing tasks and parts replacements is essential for preserving an extensive maintenance history, which can help in future troubleshooting.
Last but not least, implementing a proactive approach, including routine evaluations and anticipating upkeep strategies, enhances the reliability of product packaging machines. By adhering to these ideal techniques, organizations can make sure ideal device efficiency, lower functional dangers, and prolong tools life expectancy.

Final Thought
In conclusion, a thorough understanding of product packaging equipment elements and efficient upkeep strategies is crucial for optimal efficiency. Normal evaluations and making use of OEM parts can dramatically reduce downtime, while a well-documented upkeep history promotes aggressive care. Utilizing certified specialists better enhances repair service top quality and integrity. By applying these practices, organizations can make sure the long life and efficiency of packaging devices, ultimately contributing to boosted functional productivity and you could try this out lowered costs.
Reliable upkeep of packaging devices hinges on a complete understanding of their crucial parts, consisting of the framework, drive system, and sealing my response mechanisms.Effective operation of product packaging equipments counts greatly on routine maintenance to prevent usual concerns that can interrupt manufacturing.Implementing preventative upkeep methods is vital for sustaining the performance and integrity of packaging equipments. In addition, keeping precise documents of upkeep tasks aids in tracking the maker's performance over time, assisting in informed decision-making pertaining to future upkeep demands.
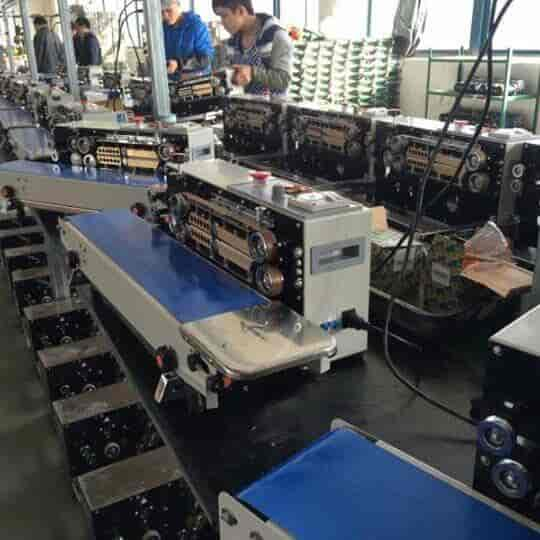
Report this page